HR Projects & Initiatives
Lafarge in Jordan is committed to developing the skills and expertise of its employees through implementing new policies and procedures and developing new training programs targeting the different categories of employees and aiming to enhance their expertise in many aspects.
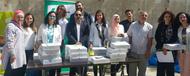
"Sehtak bel denya" initiative |
|
The Human Resources Department launched the "Sehtak bel denya" initiative, which aims to improve the individual and health of the company's employees. |
![]() |
Safety Pioneers Program |
|
Health and safety are top priorities at Lafarge Cement Jordan and this is evident across all levels of the company. By implementing stringent health and safety policies, the company strives to create a safe work environment for its employees. In turn, employees are also contributing to this environment by taking responsibly and showing their own commitment to Lafarge's "zero tolerance" policy. Lafarge is focusing through this program on four main Safety related standards:
The Safety Pioneers program, which started in 2009, strives to increase the level of employee awareness on safety issues, further encourage safe practices and implement safety procedures in order to create a safe and risk free environment. The program focuses on improving communication by encouraging employee feedback and increasing the number of reports being filed on hazardous conditions and near miss accidents in the workplace. It also develops pioneer participants to support and lead specific safety activities across the company. What distinguishes this program from other training programs is the continuous monitoring aspect of the program. Upon completion, a three month monitoring period commences entitled "Pioneer Clusters" focusing on weekly and monthly meetings with the safety teams and plant managers, in addition to meetings held with senior management to provide them with continuous feedback on the training and the challenges that the pioneers are facing. So far, four groups of 112 participants have been graduated from this program. |
Program Results:The program has witnessed a number of successful outcomes
|
Plant Operating Model (POM) Program |
|
The Plant Operating Model program defines a set of coherent principles, processes, procedures and tools that enable a given organization to function effectively and efficiently. The Operating Model focuses on the critical elements of a business in order to produce safely and reliably and at optimum cost.
The Plant Operating Model (POM) program was launched in 2010 with the aim of enhancing the performance efficiency of Lafarge Jordan's plants by creating a competent, motivated and qualified team that runs the plants professionally using proven work processes on a continuous basis.
The Plant Operating Model is based on three broad categories with 16 inter-related processes that have been previously identified and have proven to positively impact performance:
|
![]() Program Target ResultsProgram target results enable the plants to:
|
Kodorat Project |
|
By endeavouring to improve the skills of Lafarge Jordan's employees, the company launched the three-year Kodorat project aimed to develop the skills of our employees in Operations and Maintenance to enhance performance and optimize organization structure targeting Mechanical & Electrical Maintenance Technicians, CCR Operators, and Production Patrollers. Launched in 2007 and still ongoing, the Kodorat project was implemented in Fuhais and Rashadiyah plants and focused on identifying skills, training needs and future opportunities for employees through mechanical & electrical technicians multi skilling program.
The project is based on a methodology that identifies the future of each organization, defines future jobs within required competencies, identifies target groups, conducts a Gap Analysis for skills, defines training needs and launching these training Programs. |
Program ResultsAs a result, to date, the project was able to
|